Discharge Machining and Electronic Dance Music
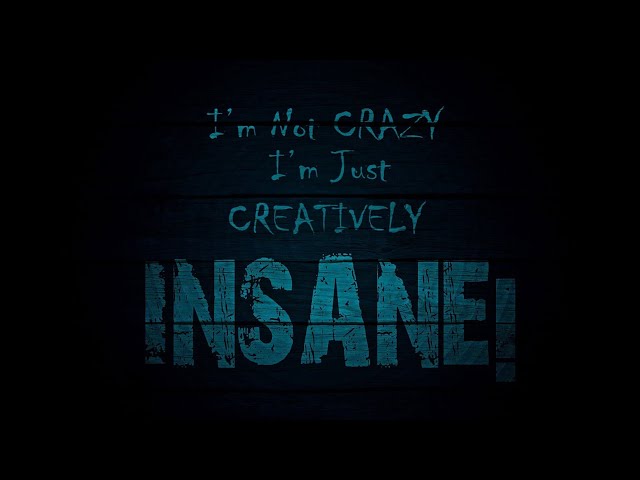
Contents
Discharge machining is a type of electrical discharge machining (EDM) that uses a high-voltage, direct current (DC) power supply. The process uses a consumable electrode to create sparks that erode the workpiece.
EDM is a type of machining that uses a high-voltage, direct current (DC) power supply to create sparks that erode the workpiece.
Introduction
Discharge machining is a process of electrical discharge that uses an electrode to remove material from a workpiece. It is often used in the manufacturing of electronic components and electronic dance music (EDM).
The process can be performed with a variety of electrodes, including:
-carbon
-tungsten
-copper
The material to be removed is generally conductive, such as:
-copper
-aluminum
-brass
What is discharge machining?
Discharge machining is a manufacturing process in which electrical energy is used to create sparks that remove material from a workpiece. This process can be used to machine conductive and non-conductive materials, and is often used to create intricate shapes and detailed designs.
Discharge machining is a versatile manufacturing process that can be used to create a wide variety of products. Common applications for discharge machining include the production of medical devices, automotive parts, and electronics.
How does it work?
Discharge machining is a process of removing material from a workpiece using electrical discharges (sparks). Material is removed from the workpiece by a series of recurring spark discharges between a negatively charged electrode and the workpiece.
The basic principles of this process were first discovered in 1770 by Joseph Priestley, who found that electric sparks could be used to erode stone. In 1808, Humphry Davy realized that the same process could be used to cut metal. The first practical discharge machining machine was built in 1851 by Robert Peel, who used it to cut hard metals such as tool steel.
Today, discharge machining is commonly used to create intricate shapes and patterns in metal, plastic, and other materials. It is especially well-suited for creating shapes that would be difficult or impossible to create using other machining processes.
Discharge machining can be used for both linear and non-linear jobs. Linear discharge machining is typically used forjobs such as cutting gears, while non-linear discharge machining is used for jobs such as engraving and sculpting.
The advantages of discharge machining include its ability to create complex shapes, its high accuracy, its low cost, and its eco-friendly nature (it does not produce harmful pollutants). The main disadvantages of this process are its slow speed and the need for a highly skilled operator.
What are the benefits of discharge machining?
Discharge machining is a process that uses electrical energy to remove material from a workpiece. It is often used to create very precise, high-quality finishes on a variety of materials.
There are several benefits of discharge machining, including:
-Very precise results: Discharge machining can produce extremely precise results, making it ideal for applications where close tolerances are required.
-High quality finish: The process can also produce a high quality finish, making it ideal for applications where a smooth surface is desired.
-Can be used on a variety of materials: Discharge machining can be used on a variety of materials, including metals, plastics, and composites.
What are the applications of discharge machining?
Discharge machining is a process that uses electrical energy to remove material from a workpiece. This process can be used to machine conductive or non-conductive materials, and is typically used to create intricate shapes or patterns.
There are two main types of discharge machining: spark and plasma. In spark machining, a high-voltage pulse is applied to the workpiece, causing a spark to jump across the gap between the electrode and the workpiece. The heat from the spark vaporizes the material, which is then blown away by compressed air. Plasma machining uses a similar process, but with a much higher voltage ( typically in the range of 10-100 kV). This voltage causes an arc to form between the electrode and the workpiece, which ionizes the gas around the arc. The ions are then attracted to the workpiece, causing them to erode the material.
Discharge machining can be used to machine a variety of materials, including metals, plastics, ceramics, and glass. It is frequently used in the aerospace and medical industries where precision machining is required.
What are the challenges of discharge machining?
Discharge machining is a process that uses electrical energy to remove material from a workpiece. It is similar to other processes such as EDM (electrical discharge machining), ECM (electrochemical machining), and PECM (pulse electrochemical machining).
The main difference between discharge machining and other methods is the way in which the electrical energy is applied. In discharge machining, the energy is transferred through an electrode that is in contact with the workpiece. This results in a series of micro-explosions that remove material from the workpiece.
Discharge machining can be used to produce very precise shapes and sizes, but there are some challenges that need to be considered. First, the process can generate a lot of heat, which can damage sensitive electronic components. Second, the process produces a lot of sparks, which can be a safety hazard. Finally, the process can produce unwanted burrs and rough edges on the workpiece.
How has discharge machining evolved?
Discharge machining is a process that has been used for many years to create electrical components. In the past, this process was often used to create simple parts such as condenser plates and heat sink mounting tabs. However, discharge machining has evolved over the years and can now be used to create much more complex parts. One example of this is the creation of electronic dance music (EDM).
EDM is a genre of music that is created by using electronic instruments and computers to create beats and melodies. This type of music has become very popular in recent years, and many EDM artists have become household names. Some of the most popular EDM artists include Skrillex, deadmau5, and Calvin Harris.
Discharge machining is often used to create the electronic components that are used in EDM music. For example, discharge machining can be used to create circuit boards, which are then used to control the sound of the EDM music. Additionally, discharge machining can be used to create LEDs, which are often used to add visual interest to EDM performances.
Overall, discharge machining has come a long way from its humble beginnings. This process is now being used to create some of the most complex parts that are used in electronic devices and music genres.
What is the future of discharge machining?
There are many possible future developments that could occur in the field of discharge machining. One possibility is the development of more effective and efficient cooling methods. This could allow for higher machining speeds and greater precision. Additionally, new ways to create spark gap geometries could lead to more complex and intricate designs being machined. Finally, the use of discharge machining in the creation of electronic dance music (EDM) could become more widespread.
Conclusion
In conclusion, discharge machining can be used to create Electronic Dance Music. This is a popular form of music that is enjoyed by many people around the world. This type of music can be created using various types of equipment, but the most important factor is the quality of the sound.